Overview
Hot rolling is an important processing method of nickel alloy / superalloy (hereinafter collectively referred to as superalloy). Its function is to change the size and shape of the alloy by extrusion to meet different needs.
The processing range of hot rolling is large, and the processing deformation is large. Some superalloy materials (such as plates and thick-walled pipes) have great resistance to deformation due to their relatively large thickness and size. They cannot be deformed by cold working (cold rolling, cold drawing), and can only be deformed by hot rolling method. Therefore, hot rolling plays an irreplaceable role in metal processing.
In this article, AEETHER will use popular language and graphic illustrations to illustrate the principle of hot rolling, the effect of hot rolling on product performance and the precautions for hot rolling. The pros and cons of hot rolling and cold rolling will be listed at the end of the article.
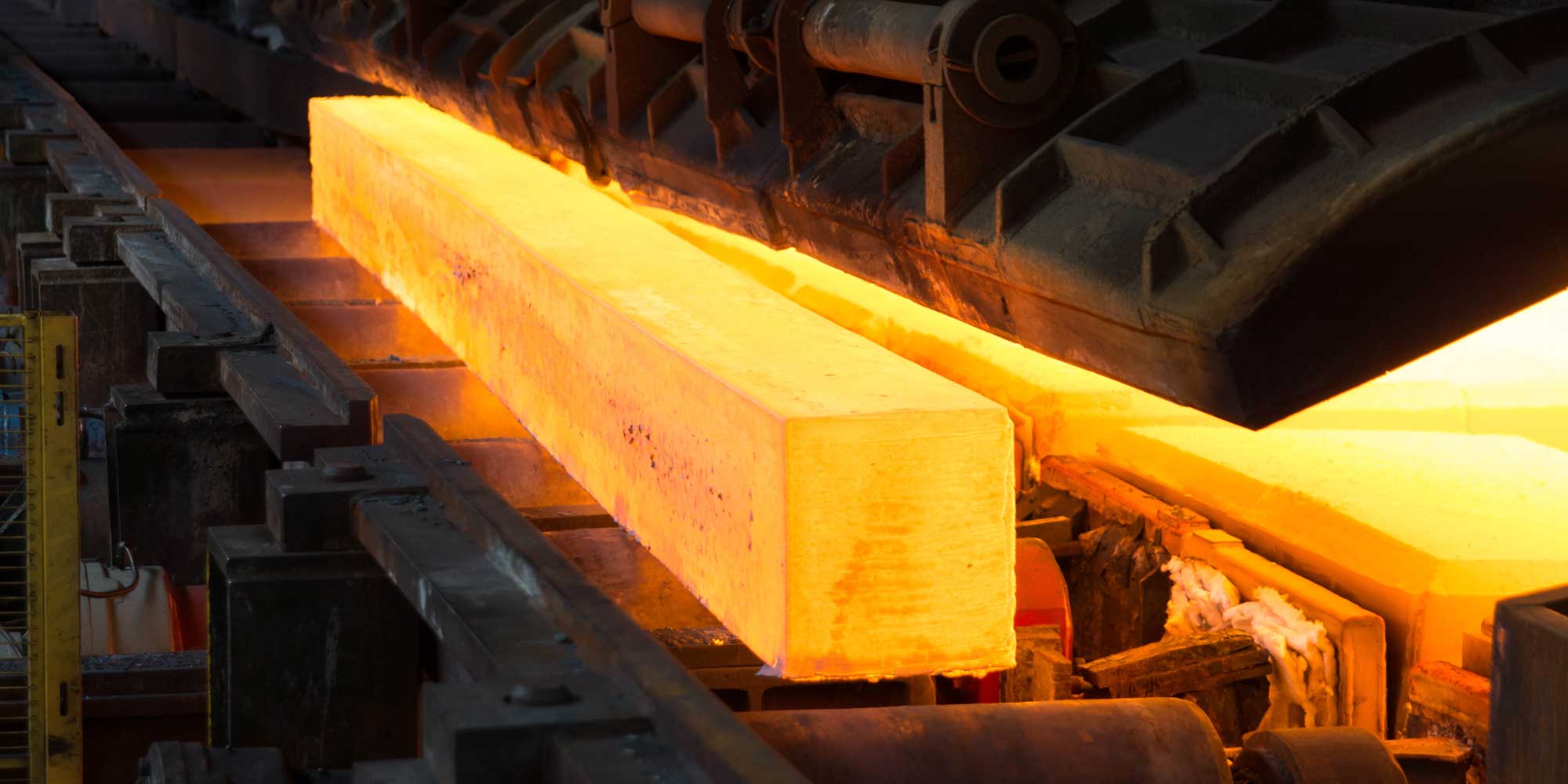
The Principle of Hot Rolling
Hot rolling refers to the rolling process of superalloys above the recrystallization temperature. During rolling, the rolls squeeze the alloy to plastically deform the metal. Recrystallization refers to the process in which the old crystal structure decomposes and new crystal grains are generated at the same time when the superalloy is heated to a certain temperature.
Different metal materials have different recrystallization temperatures, so hot rolling has nothing to do with absolute temperature, but is related to the recrystallization temperature of each alloy. As long as it is above the recrystallization temperature and below the initial melting temperature, the rolling process is called hot rolling (as shown in Figure 1).
Since the hardness of the superalloy decreases above the recrystallization temperature and the plasticity increases, there can be a large amount of deformation during the rolling process. Hot rolling is generally used for products with large cross-sectional dimensions, large deformation, and difficult processing at room temperature.
Temperature
Temperature
Superalloy Hot-rolled Plate
The superalloy hot-rolled plate refers to a plate with a thickness of 2.5mm or more. Due to the relatively thick thickness, it is generally manufactured using a hot rolling process. The principle of hot-rolled plate is shown in Figure 2 and Figure 3:
Superalloy Hot-rolled Bar
All the superalloy bars must be hot-rolled first, and smaller-sized rods can be cold-drawn to reduce the diameter. The principle of hot-rolled round bar is shown in Figure 4 and Figure 5:
Superalloy Hot-rolled Pipe
Ordinary superalloy seamless pipes are manufactured by cold rolling or cold drawing, but the thick-walled superalloy pipe needs to be manufactured by hot rolling due to its thicker wall. The principle of hot-rolled superalloy thick-walled pipe is shown in Figure 6 and Figure 7:
The Effect of Hot Rolling on Alloy Properties
Work Hardening and Recrystallization
In the article about cold rolling, we mentioned that the rolling process will cause grain extrusion and deformation, which will cause the alloy material to harden and increase the brittleness. In hot rolling, rolling can also cause this work hardening. However, because hot rolling is rolling above the recrystallization temperature, the extruded and deformed grains will decompose to form new grains, so that the structure of the alloy is restored to the original stable state, and there will be no hardening effect. In other words, the work hardening effect of hot rolling and the softening effect of recrystallization cancel each other out.
Grain Refinement
Hot rolling can break the coarser grains into finer grains, so as to achieve the effect of grain refinement. The fine grains can improve the mechanical properties of the alloy at room temperature. It is worth mentioning that since most superalloys work at high temperatures, increasing the mechanical properties at high temperatures requires large grains instead. Therefore, most of the fine-grained superalloys need to be heat-treated to form coarser grains.
Increase Density
In the refining process of superalloys, some pores will inevitably appear. These pores will have a certain impact on the mechanical properties of the alloy. Due to the higher temperature of hot rolling, the atomic movement in the alloy is more violent, and these atoms will fill these pores. Improve the density of the alloy, so as to achieve the effect of improving the mechanical properties of the alloy.
Multiphase Alloys Form a Ribbon Distribution
In some multiphase alloys (such as Monel K-500, Inconel 718, Inconel X-750, Incoloy A-286, etc.), in addition to the solid solution strengthening phase γ phase of the superalloy itself, there will also be precipitation strengthening phases such as γ' phase and γ'' phase. In the hot rolling process, these phases will change from the original dispersion distribution to the band-like distribution in the direction of deformation. This distribution not only reduces the strength of the alloy, but also reduces the plasticity and impact toughness of the alloy, which is extremely detrimental to the performance. This distribution can be eliminated by normalizing or annealing.
Precautions for Hot Rolling of Superalloy
The Temperature Range of Superalloy Hot Rolling
As mentioned above, hot rolling refers to rolling performed above the recrystallization temperature and below the initial melting temperature. But the actual situation is not that simple. The degree of alloying of superalloys is very high, especially precipitation-strengthened superalloys are added with aluminum and titanium elements with lower melting points. This results in a much lower initial melting temperature of the superalloy than ordinary steel.
On the other hand, due to the increase of solid solution strengthening elements (such as: chromium, molybdenum, cobalt, tungsten, niobium, tantalum, etc.). The bonding force between the atoms of the alloy increases, and the atoms are more difficult to diffuse, which leads to a higher recrystallization temperature of the superalloy than that of ordinary steel.(Figure 8)
Temperature
Temperature
Temperature
Temperature
The above two reasons cause the hot rolling temperature range of superalloy to be much smaller than that of ordinary steel. Not only that, there is also an overheating temperature between the recrystallization temperature and the initial melting temperature. Above the overheating temperature, the crystal grains will grow up quickly, and the large crystal grains will cause the high temperature strength of the alloy to increase and the plasticity to decrease, making it difficult to roll and deform. Therefore, the hot rolling of superalloys needs to be controlled below the overheating temperature (Figure 9).
Temperature
Temperature
Temperature
Deformation Degree of Superalloy Hot Rolling
Since the superalloy is an alloy designed to increase the high-temperature strength, the high-temperature plasticity of the alloy is also reduced, so the hot-rolling deformation of the superalloy is smaller than that of the steel.
Deformation Resistance of Superalloy Hot Rolling
The good high-temperature strength of superalloys results in a relatively large deformation resistance at high temperatures. Therefore, when hot rolling superalloy materials, it is necessary to choose rolling equipment with greater strength and pressure.
Deformation Speed of Superalloy Hot Rolling
Deformation speed has a significant effect on the hot rolling performance of superalloys. With the increase of deformation speed, the softening effect of recrystallization is too late to completely eliminate the work hardening effect, resulting in an increase in deformation resistance and a decrease in plasticity, and the hot workability becomes poor. The speed of the rolling mill in hot rolling is about 10mm/s. This processing speed needs to be changed with the degree of alloying of the alloy. The higher the degree of alloying, the higher the deformation resistance of superalloys, we need to reduce the processing speed of these superalloys. The deformation speed of the superalloys with a low degree of alloying can appropriately increase.
Comparison of Hot Rolling and Cold Rolling
The following table is a comparison of the advantages and disadvantages of cold rolling and hot rolling:
Hot Rolling | Cold Rolling | |
---|---|---|
Precision | ✔ | |
Deformation | ✔ | |
Mechanical Properties | ✔ | |
Effectiveness | ✔ | |
Size Range | ✔ | |
Surface Smoothness | ✔ | |
Uniformity of Wall Thickness | ✔ |
Conclusion
Hot rolling is rolling above the recrystallization temperature and below the overheating temperature. Generally, alloys with larger and thicker sections need to be deformed by hot rolling. Hot rolling can improve the properties of the alloy to a certain extent. In order not to produce work hardening during hot rolling, it is necessary to appropriately reduce the deformation speed.
AEETHER CO., LIMITED produce nickel alloy hot-rolled thick-walled pipes, hot-rolled plates, and hot-rolled bars. If you have any requirements, you can send inquiry to our E-mail: